在线ORP检测仪检测值持续异常(如数值漂移、偏离标准范围或无响应),会直接影响化工生产的工艺调控。这类问题需从仪器本身、检测环境、样品特性三个维度逐步排查,结合 “故障定位 — 针对性处理 — 验证效果” 的逻辑解决。 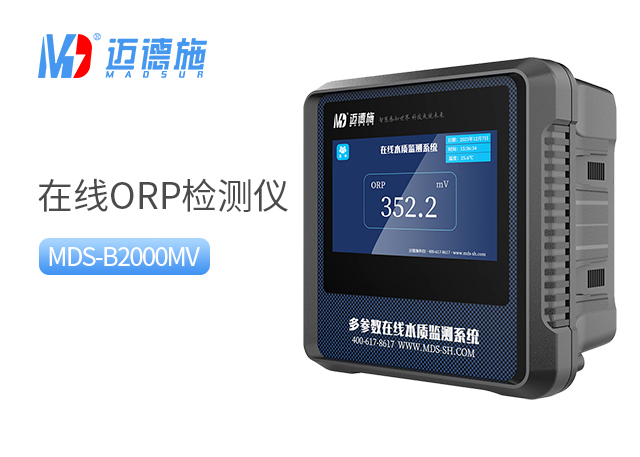
一、优先排查仪器核心部件故障 ORP 检测仪的异常常源于电极或电路系统问题,需重点检查: 电极性能衰减或污染:电极是检测核心,若敏感膜附着油污、结垢(如化工废水中的有机物、金属氧化物),会阻碍电子传递,导致读数漂移。可先取下电极,用软毛刷蘸去离子水轻刷表面,再用 0.1mol/L 稀盐酸浸泡 10 分钟(去除无机垢)或 3% 过氧化氢溶液浸泡 5 分钟(去除有机污染物),冲洗后重新安装。若电极使用超过 6 个月,需检查敏感膜是否破损 —— 破损会导致内部电解液泄漏,需直接更换电极(新电极需在 3mol/L 氯化钾溶液中活化 24 小时后使用)。 电路与接线问题:接线松动或氧化会造成信号传输不稳,表现为数值频繁跳动。需关闭仪器电源,检查电极与主机的连接端子,用无水乙醇擦拭氧化层,重新插拔并拧紧接口。若使用过程中曾发生水样泄漏,需检查电路模块是否受潮,可打开主机外壳用吹风机冷风吹干(避免高温损坏元件)。 二、优化检测环境与安装条件 环境干扰是易被忽视的诱因,需针对性调整: 温度与流速波动:ORP 值对温度敏感(温度每变化 1℃,读数可能偏移 1-2mV),若检测点靠近换热器或冷水机组,需加装恒温装置(如水浴套),或将电极移至温度稳定区域。此外,水样流速过快(>1m/s)会冲刷电极表面,形成湍流干扰;流速过慢则易积累气泡。需调节流通池阀门,将流速控制在 0.3-0.5m/s,同时确保电极安装位置无气泡滞留(可倾斜安装电极,让气泡自然上浮)。 电磁与化学干扰:化工车间的电机、泵体产生电磁辐射,会干扰电信号。可将电极线缆更换为屏蔽线,并远离强电设备(距离≥1 米)。若水样中含高浓度离子(如氯离子>1000mg/L)或氧化剂(如臭氧),会引发非目标氧化还原反应,需在检测前加装预处理装置(如离子交换柱)去除干扰物质。 三、通过校准与验证确认恢复效果 处理后需通过校准验证是否解决问题: 重新校准仪器:用标准缓冲液(如 200mV、400mV ORP 标准液)校准 —— 先将电极放入 300mV 标准液,待读数稳定后按 “校准” 键;再换用另一浓度标准液验证,误差需≤5mV。若校准失败,需检查标准液是否失效(标准液需冷藏保存,开封后 1 个月内使用),更换新标液重试。 现场水样比对:校准后取正常工况下的水样,用便携式 ORP 检测仪同步测量,两者读数偏差应≤10mV。若偏差仍大,需检查工艺是否存在异常(如原料配比变化导致水样成分改变),结合生产参数进一步排查。 解决在线ORP检测仪测量值异常的核心是 “先排除硬件故障,再优化环境干扰”。日常需建立维护记录,记录电极更换时间、校准结果及异常处理措施,通过规律维护(建议每周清洁电极,每月校准一次)预防持续异常,确保为化工生产提供可靠的电位数据。
|